近些年來,隨著電子設備向輕薄化、小型化發展的趨勢愈加明確,電子產品對PCB的高密度和高性能需求越來越突出。提高利用率、縮小板間距離,增加產量成為行業大勢所趨,受到這些因素的影響,傳統PCB機械分板法變得不切實際了,且成本增高,效益會變低。
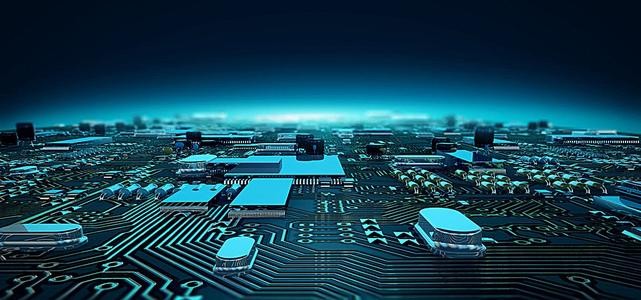
激光切割技術的出現,為PCB分板帶來了革命性的變化,其具有切割間隙小、精度高、熱影響區小、無應力、切割邊緣整齊光滑、操作靈活度高等明顯優勢,解決了傳統加工方式弊端的同時,還能更好地滿足PCB制造商在加工工藝和成本等方面的嚴苛需求。
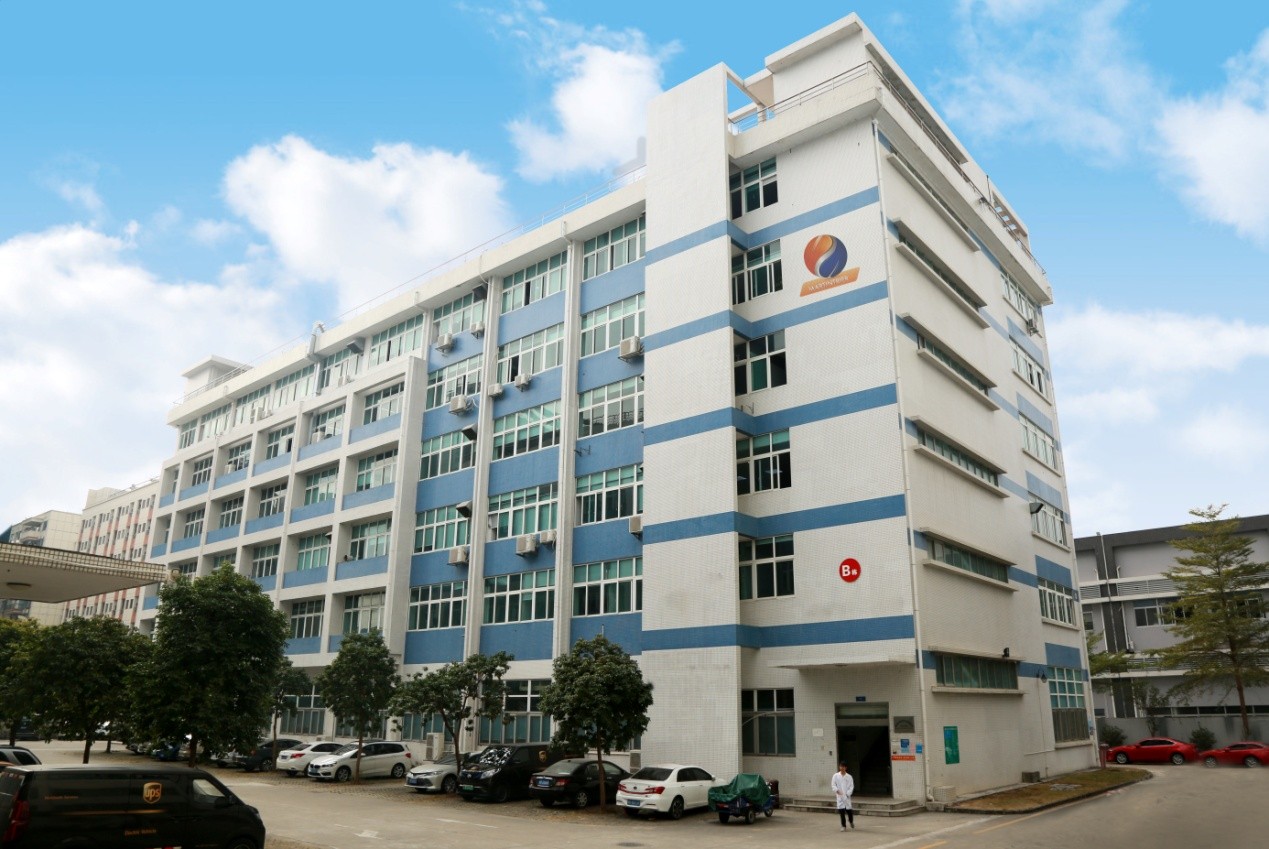
應對這一需求,激光行業及自動化的技術先行者——馬丁特尼爾以需求為目標,以開發市場為己任,長期專注于SMT行業。目前已打造出一支精銳的高端人才團隊,不斷進行技術創新,引領行業技術升級,積極進取不斷創新,從而推出了激光切割機、電路板切割機等一系列高端激光切割設備。推動先進工業級激光器的國產化,為中國高端制造業注入新的活力和生機,在國內以至國際電子制造及裝配領域中享有崇高的聲譽。
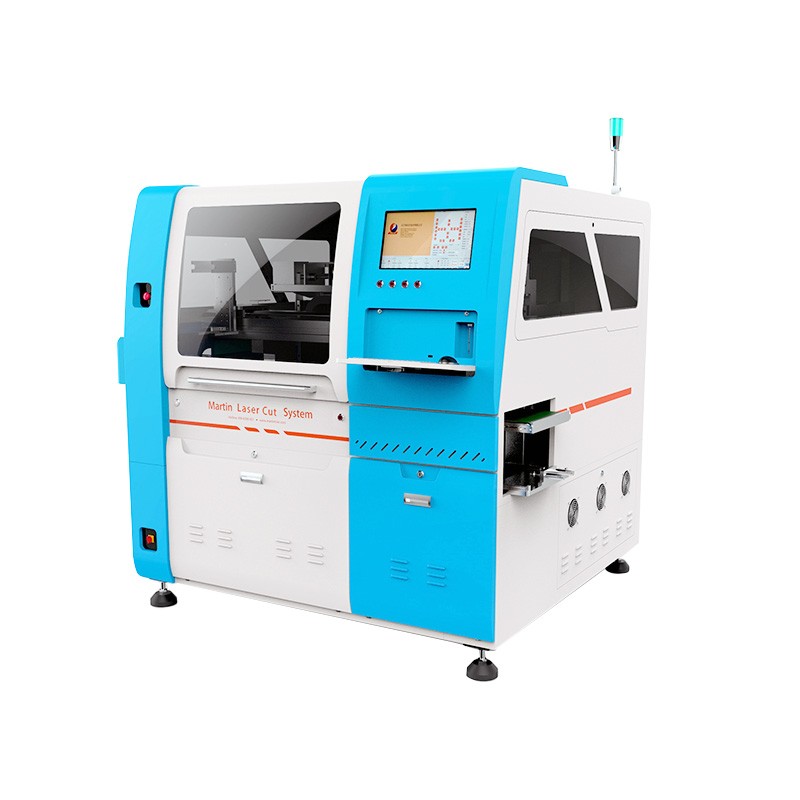
其中,馬丁特尼爾新型激光切割設備——MicroCut1200系統一經推出便贏得業內專家高度認可,極大提升產能和良率,降低行業客戶運營成本。功能強大的MicroCut1200系統憑借著優越的性能、高性價比、激光切割技術優勢等決定性的因素,而在電子、醫療、精密配件等領域應用廣泛。
這一系統采用了無接觸切割工藝,明顯提高對PCB分板的控制能力,確保精密、貴重元器件、焊錫連接敏感基板不會在分板過程中承受機械應力的沖擊;系統還使用了計算機數據驅動加工,可以完全省去模具、工具費用,提高質量,實現極低的運行成本;此外,MicroCut1200系統更好地利用寶貴的拼版空間,切割縫及元器件之間的間距可以做到很小,元器件可以更緊靠邊緣放置,電路板可以做得更小,更輕,常用于對切割質量要求較高的工件加工之中,為電子產品的升級精進創造了不可或缺的先決條件。
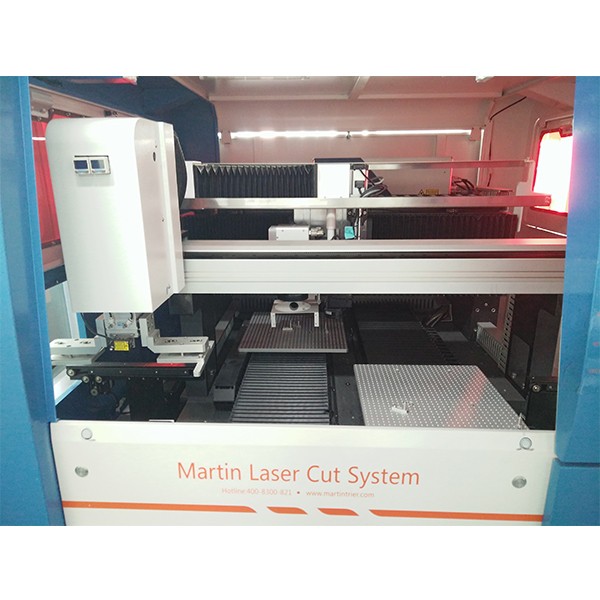
過去,傳統的去除粉塵、碳化等缺陷往往都需要增加機械打磨或者拋光工序,還可能需要運用化學藥水,既不環保,又格外耽誤時間。MicroCut1200系統憑借獨特的吸塵系統設計,可以全方位高效地收集加工時產生的粉塵,充分保護被加工產品的潔凈度,還能避免對工作環境的污染,更使得器件長期處于清潔狀態,不需要頻繁維護。特有的專業加工程序,使得切割輪廓定位精準,無耗材,無殘留。
當下,追溯系統作為一種可以對產品進行正向,逆向或不定向追蹤的生產控制系統,目前已被廣泛應用于各個行業中,適用于各種類型產品的生產和控制。MicroCut1200系統便設置了標準工業接口,可集成到MES系統中,支持操作數據的收集,機器分配,產品追溯、跟蹤及配送監控,避免人工誤貼、錯貼、誤印,實現了SMT生產線上產品的自動化、智能化的信息追溯,讓制造商在激烈的競爭中隨時隨地更好地了解自身企業的發展與“健康狀況”。
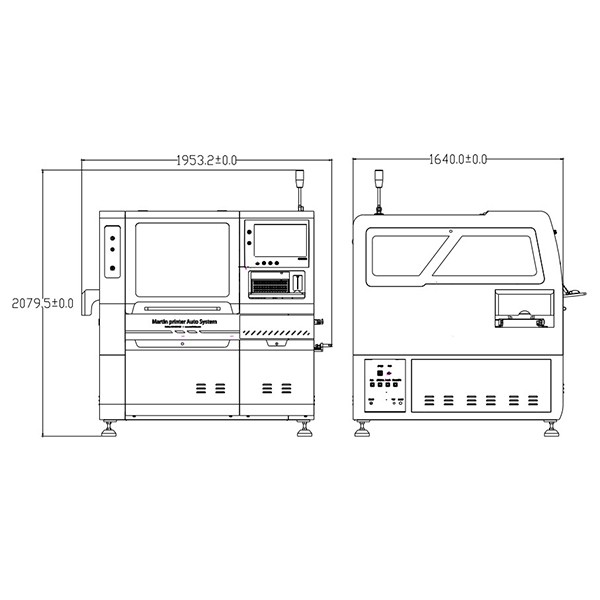
智能制造時代下,激光分板技術已經帶來了諸多優勢,PCB制造商已經將這項技術發揮到了極致。馬丁特尼爾MicroCut1200系統的出現,無疑打開了更開闊的視野,充分滿足了當下電子和汽車行業當前及未來的要求,凸顯出公司自身的激光分板技術優勢,既適用于以質量、效率、成本優勢對傳統機械加工技術進行更新換代,也能滿足國際頂尖機構各種高端產品需求,已然成為尖端科技與精密制造的聯結橋梁。